Two Reproductions of c. 1929 Exterior Lanterns
Palm Beach, Florida
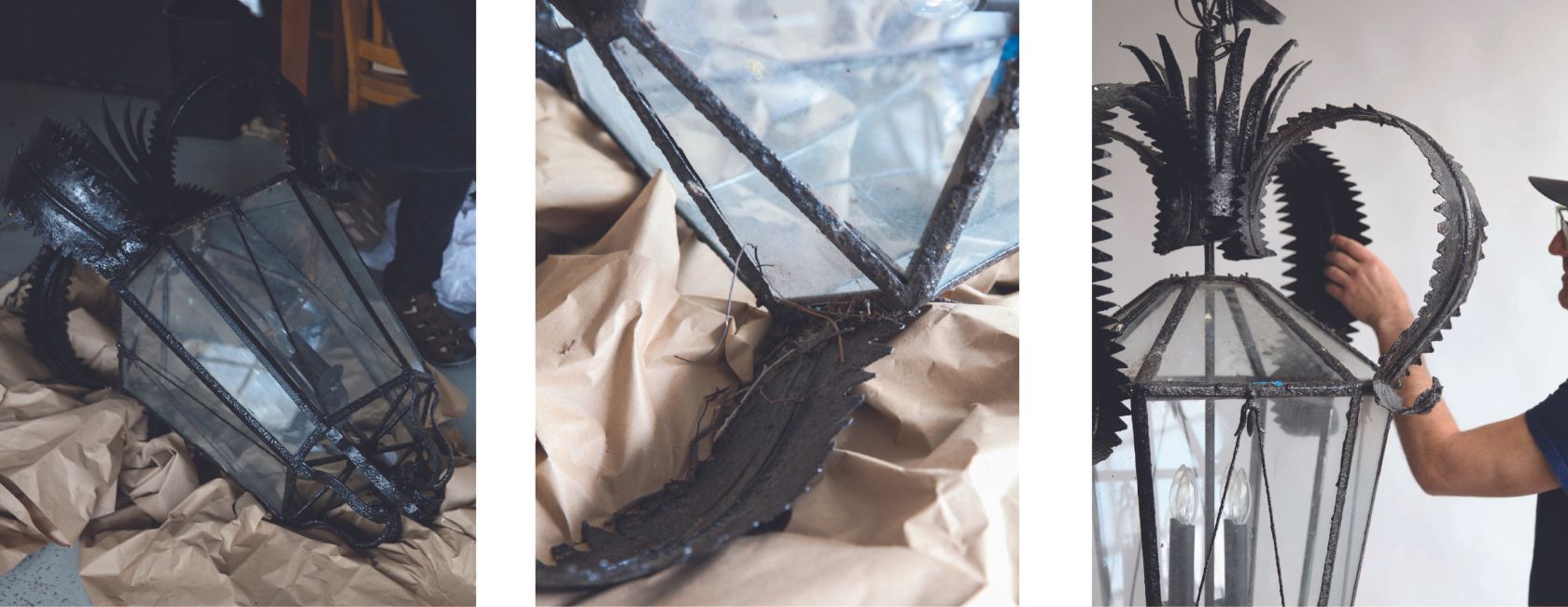
A 24,000 square-foot, 1929 landmarked jewel of an estate on Ocean Drive in Palm Beach is the installation site of the project for two sets of antique lantern reproductions, the recipient of the 12th Annual Addison Mizner Award for Craftsmanship.
A tapered, beveled rectangular lantern was reproduced in a quantity of one. It was affectionately nicknamed “Maleficent” by the design engineer while drafting the large horn-like leaves that would be snipped and hammered by hand. The other, a maritime-themed round, tapered, lantern detailed with twisted rope ladders and surmounted by a painted flag, was reproduced in a quantity of four. Both types required us to flex a breadth and depth of expertise in metal and glass-working and finishing techniques.
Compound curves a-plenty, each was cut from flat sheet and formed individually, heavily relying on some of the shop’s oldest forming tools (c. 1910 sheet roller) and an operator who developed the order of steps that resulted in natural, curling foliage to closely mimic the 1920s’ original.
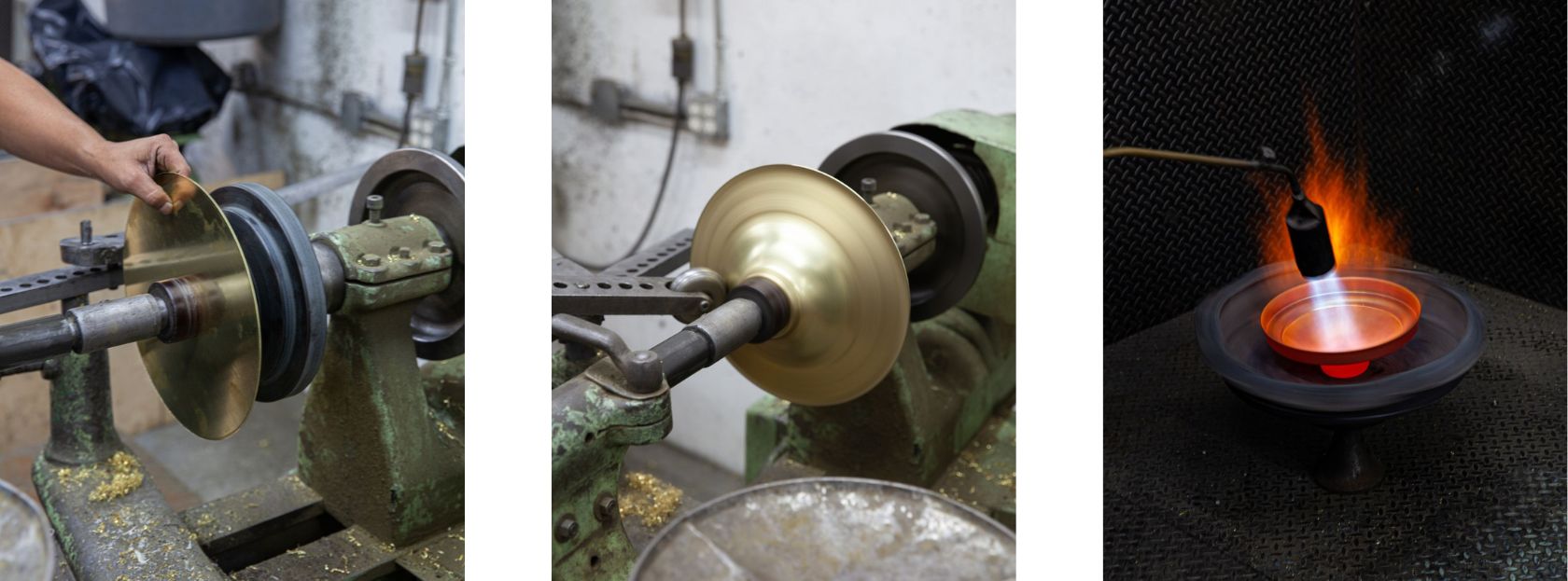
Another metalforming technique used was spinning. Shown is the brass sheet being sheared to size (above left), spun over a custom chuck (middle) and torch-annealed to prevent cracking after work-hardening (above right).
Twisting 5/16” brass bar around itself on the lathe gave us braid bands which were rolled to the correct radius and brazed together.
Preparation is the key to a finish with character and longevity. We create and prepare sub-assemblies of parts where possible. Rather than finishing each individual part and then assembling and joining, parts can be joined in fabrication for ease and quality of finishing and final assembly. Shown above are bodies being soldered for assembly (at left) and in the sandblasting machine to receive a preparatory satin (right) and, further, emerging from the browning acid patina (below left).
Making a verdigris patina with natural variegation is a multi-step process. The rope ladders shown in the middle image above illustrate three stages: sandblasted, browning/blackening patina, and greening verdigris patina. Still remaining for the verdigrised rope ladder is a buff with butcher’s wax which leaves a soft sheen and increases dimension of the custom metalwork’s fine details.
The originals in the rough state they were received by us: beyond repair for re-installation in a site with salt air and high winds.